The concept of low-cost housing in India elevated in 1989, with the construction of Aranya, a low-cost housing proposal, 6 kilometres from Indore, by Balkrishna Doshi. The question of ownership is fundamental to B.V. Doshi who famously verses ‘building homes is about creating a sense of belonging, about participatory involvement and about the expression of aspirations, relationships and desires’.
Low-cost housing scheme in India is to help shelter the Economically Backward sections (EWS), slums and street dwellers and the underprivileged in a way wherein a framework and access to serviced land is provided rather than a finished house. Over time, this house grows into home as per the requirements and needs of the occupants; they are allowed to design it the way they want and what suit their needs the best, from shared outdoor spaces and courtyards to an outdoor staircase leading towards interiors.
With the rising popularity of low-cost housing, there was a lot of research done on how this scheme could be more wide-spread and efficient, catering to more almost 65% on the rural and under-privileged population of India. What concerned the efficiency of low-cost housing the most was the construction material usage and their modification, different construction elements such as slabs, beams, columns etc.
Material type, usage and cost variation
Cost on material for low-cost housing drastically reduces compared to building finished houses since the material is to be taken in bulk and should be the one that is locally available. Cost on labour too can be reduced by keeping steady hours of working for a specified time period.
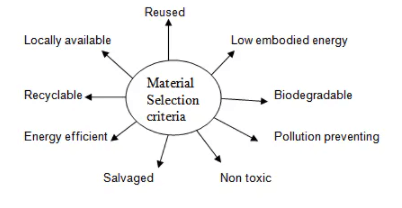
(Characteristics of materials used for low-cost housing)
1. Materials from Recycled Waste
Materials such as aggregates from concrete can be recycled and can be used to construct partition walls. In case of bricks, they too can be broken down into small aggregates either to manufacture other bricks or even as landscape elements. In case of wood waste, it can be recycled to manufacture plywood or soft boards.
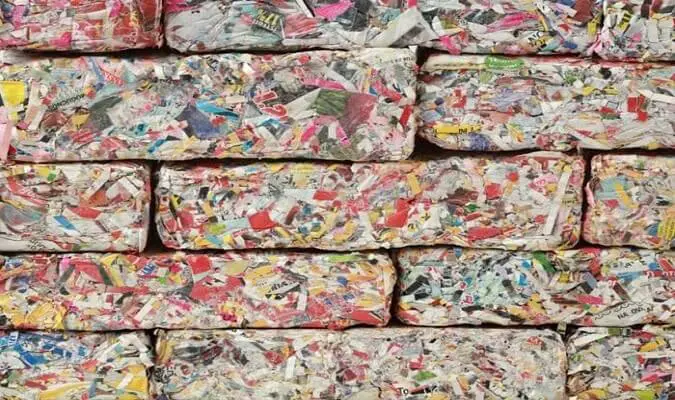
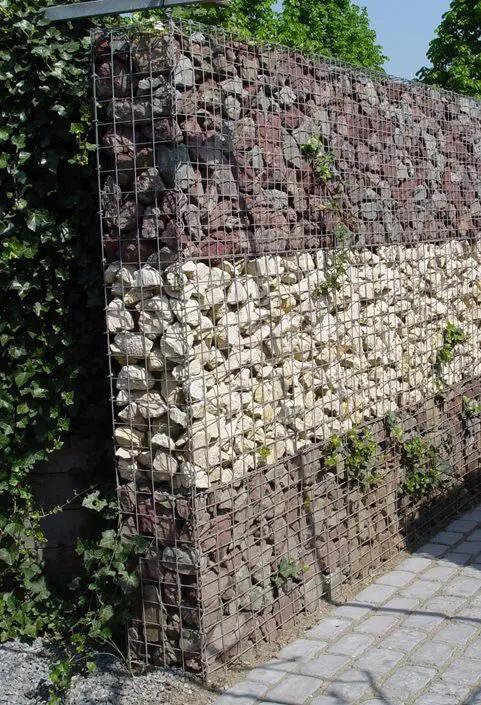
Bricks from recycled paper mesh and mud
Gabion wall from recycled aggregate
2. Concrete Blocks
These are manufactured and fabricated at factories and have the option of being solid of hollow from within, depending on the usage. These can be used for foundations, external walls, partition walls. The hollow bricks can be strengthened by insertion of steel rods.
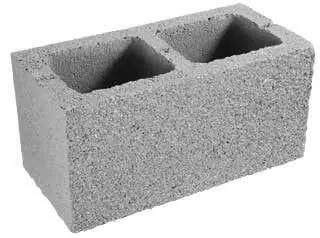
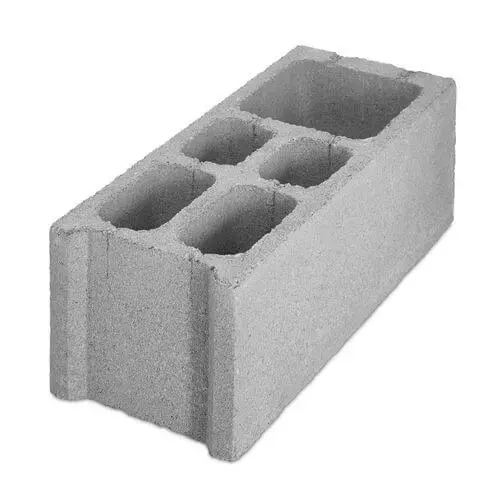
Advantages:
- These are generally light-weight, durable, and fire-resistant.
- Since they’re made from cement, they are termite resistant, sound proof, and provide natural insulation.
3. Mud bricks reinforced with Natural Fibers
These natural fibres make an excellent replacement for steel reinforcements and can be obtained from straw and palm and coconut tree leaves). This is the most preferred material in dry and humid rural region, to make houses weatherproof.
A coating of sulphur is preferred over the bricks to make it water-resistant. Other available types of fibres are bagasse, corn straw, rice husk etc. These can be combined with cement to make them corrosion resistant.
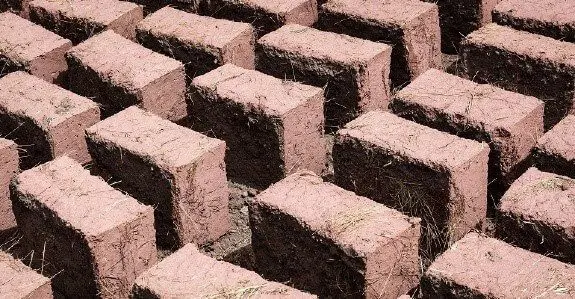
Sun-dried Mud bricks reinforced with straw fibres
Advantages:
- High strength and durability
- Natural fibres increase the strength
- Locally available, lesser energy consumption compared to baked bricks
4. Magnesium Oxide cement
It is also referred to as ‘eco cement’ since it is composed of several waste, recycled and upcycled materials mostly obtained from magnesium mining. But due to its less water resistance, it is preferred only in dry and humid regions.
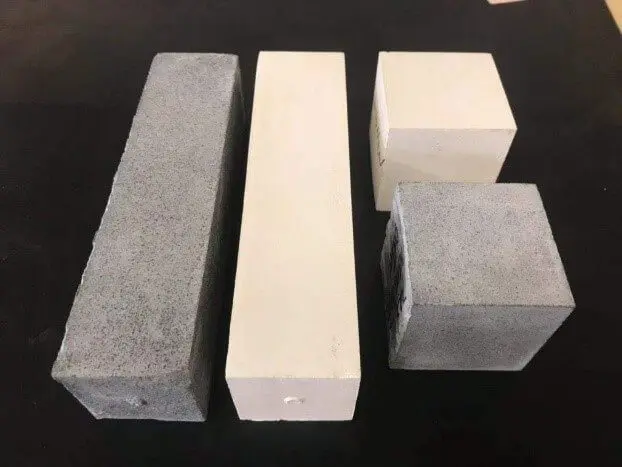
Advantages:
- It requires about 20-40% lesser energy than what is required for production of Portland cement.
- It has no side effects on the humans residing inside the house.
5. Prefabricated Components
This is by far the most commonly used method to construct permanent or long-lasting houses and structures. It forms an exceptionally well and cheaper replacement for brick and mortar type of construction. Components such as slabs, columns and even roofs are manufactured or pre-fabricated at factories off-site ad then assembled on site. Materials can vary from steel to cement to wood.
Advantages:
- Components can be customised based on needs and requirements of the tenants.
- Though this method is a little expensive than other methods, it offers high level of efficiency, decreased labour cost and efficient time management.
- Auxiliary activities such as wiring, plumbing, and plastering during the casting stage are eliminated.
Areas where cost can be reduced
- Usage of locally available material or other sustainable materials like lime or soil cement blocks instead of red baked bricks
- Usage of materials that consume or require less energy both before and after construction.
- Reduction of plinth area by using thinner wall concept
- Usage of environment-friendly materials that last longer with least maintenance like concrete door and window frames instead of wooden frames.
- Pre-planning of components of house, reduction in quantities and dimensions as in where required. If the component is not necessary or can be replaced using a more efficient component then follow the same.
Here are few examples which explains the evolution of low cost housing in India and how it has helped communities set-up ‘homes’ over the years.
– Janvi Mangukiya