With the rise of new Construction technologies, Environmental concerns suggest Low Carbon Strategies as an ultimate solution. The Human population is projecting towards outnumbering the natural resources with increasing demands.
Construction Industry emits large-scale carbon content every year through industrial production, transportation, consumption of fossil fuels, and even respiration. Low Carbon Strategies focuses on managing and reducing the carbon footprint to achieve environmental sustainability and cost benefits with increased revenues.
Technological Advancements are adapted through Green Building Ideologies to counter the negative impacts of Climate change. Green Buildings with par LEED scores improves running costs and raised property value by reducing Carbon Footprint.
What is Carbon Footprint?
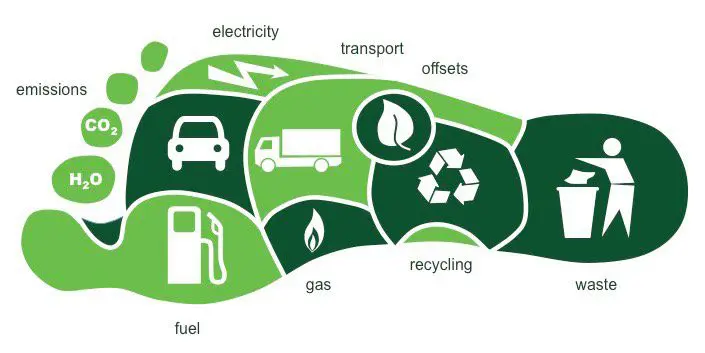
Carbon Footprint refers to the measure of the carbon dioxide produced during an activity or the existence of an entity. Carbon Dioxide affects the environment through global warming. Carbon Footprint is measured as tonnes of CO2 produced.
In the case of the houses we live in, carbon footprint accounts as follows:
- Embodied energy: It is the amount of energy utilized for constructing the structure.
- Operational energy: Refers to the amount of energy required for functioning the house.
These two energy factors are responsible for the emission of greenhouse gases. It is not only the construction phase of the house which contributes to carbon emissions. But, we need to realize that improper planning for the future operations of the house can result in drastic changes.
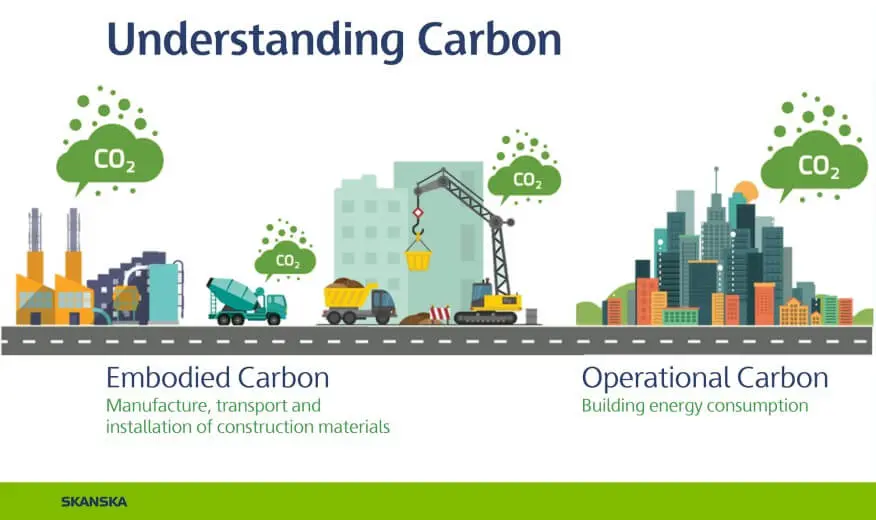
Considering the energy factors and phases for the construction of houses, the following set of points can be helpful to reduce building’s carbon footprint:
1. Strategising Early
A building’s design and construction phases should be pre-evaluated and pre-planned. This stage optimizes the reduction in the production of carbon emissions. Early planning can propose alternative layouts, refined details, and substituent materials to counter carbon loads.
Architects can assess future operational loads while iterating during the early design stage. The life cycle assessment of the product includes all the flow management (energy, water, waste, production, and materials) to calculate sustainability.
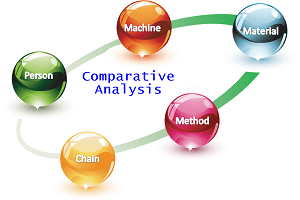
Pre-planned designs can suggest a comparative analysis of materials and their impact on the structure. This data compilation combined with iterations can help to reduce the overall carbon footprint of the building.
2. Managing H.V.A.C (Heating, Ventilation, Air Conditioning) Loads
HVAC systems work on electricity or fossil fuels to regulate the building’s internal environment. It is not easy to eliminate mechanical systems in maximum cases but reducing their loads can be a solution. HVAC contributes to 40% of carbon emissions.
So, regular maintenance and scheduled off-hours must be a priority to maintain the efficiency of the mechanism.
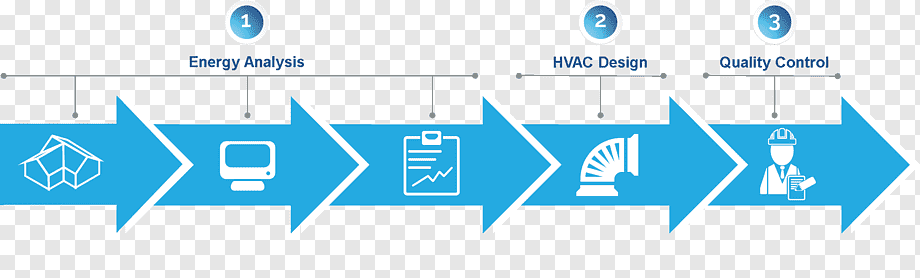
Efficacy is not just about managing the existing HVAC loads. New proposals need to assess the requirement and suggest alternative passive techniques to minimize the HVAC loads.
3. Control Through Insulation
Most of the buildings that require mechanical ventilation tend to have a heavy carbon footprint. So, Insulation can restrict internal thermal loss to the exterior environment. It saves energy and reduces the carbon footprint. Simple construction details and building orientation can control thermal loss and save on heavy bills.
During the construction phase, it is advisable to place heavy machinery insulated from heated environments to ensure efficient working. Installing Machinery that dissipates heat in heated environments can reduce workability.
4. Lighting
The lighting scheme of a building defines its electrical loads. These electrical loads contribute heavily to the carbon footprint of the building. It is advisable to plan the lighting program of the building to attain optimizable natural light and solar thermal gains.
These factors can be adjusted through planned fenestrations and orientations. Architects should maintain the solar gains such that:
In summers, they do not cause overheating.
In winter, the building does not require any mechanical heating.
5. Recycling As a Medium
Architects and Clients should be encouraged to source recycled building materials while construction. Recycling reduces the impacts of carbon footprint through reduced mining for newer resources.
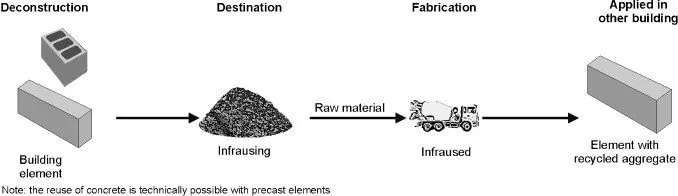
Steel has been the most recycled material in the construction industry.
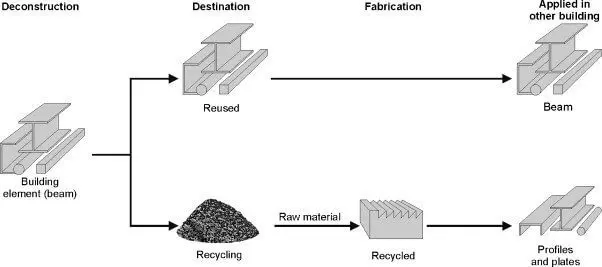
Clients should opt for Green material suppliers who embrace environment-friendly practices as vendors.
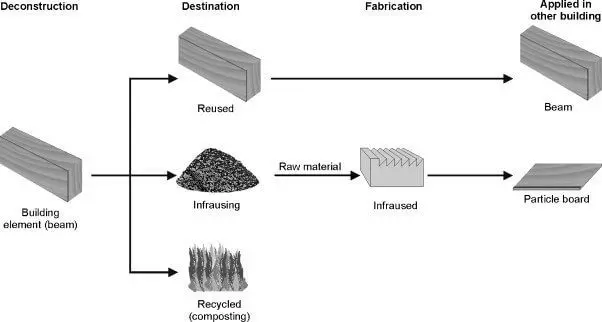
6. Using Prefabricated Materials
Prefabricated material components are manufactured under regulated conditions that reduce carbon emissions during production. These components have improved quality and produce less trash. Manufacturing components at the site results in dealing with the harsh conditions which reduce efficiency resulting in increased carbon emissions.
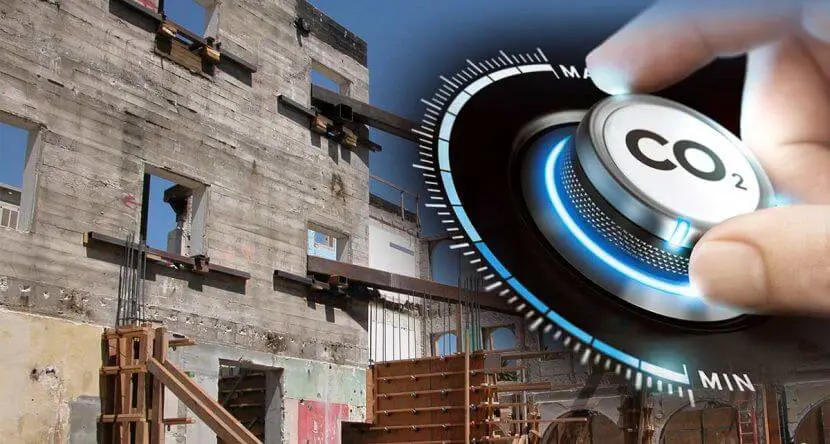
Prefabricated materials improve the quality of work with precision. And also minimizes assembly time through pre-planned mechanisms and low equipment use.
7. Managing Construction Waste
Construction processes and their by-products are interrelated in a vicious cycle of carbon emissions. Waste Management on-site and off the site require disposal processes that contribute to the Carbon footprint of the building construction process.
It is advisable to manage a majority of the construction waste on-site to avoid transportation. Waste management can include reusing the scrap as filler materials.
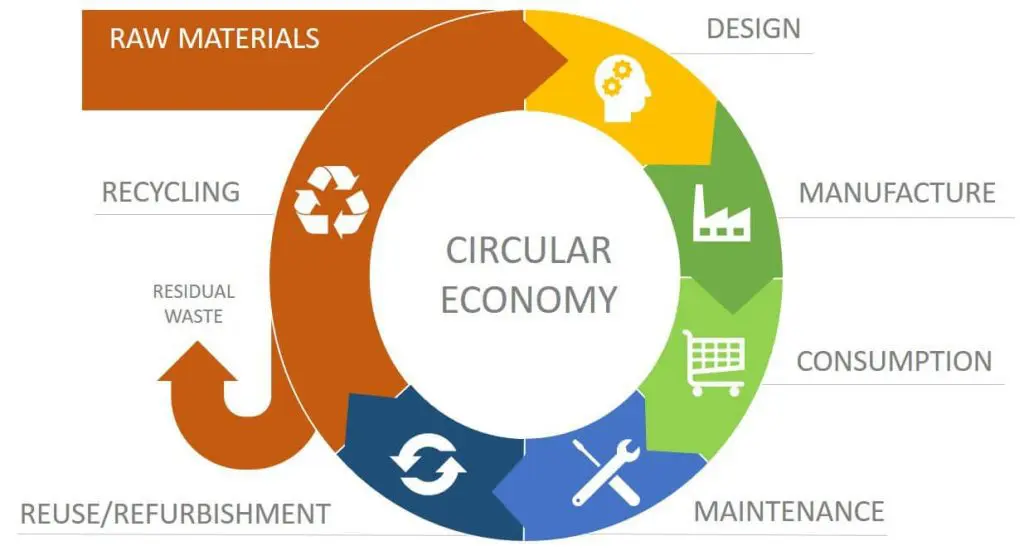
8. Adopting Lean Manufacturing
Lean manufacturing is a method of maximizing productivity and minimizing wasteful activities in construction. This leads to reduced operational losses and promotes a low carbon strategy.
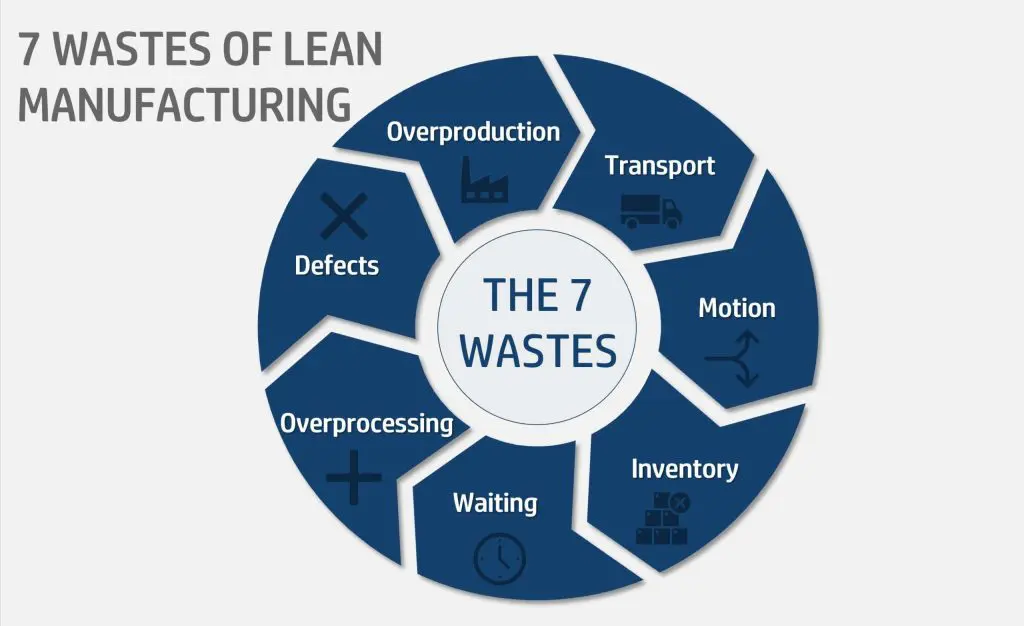
The majority of Lean manufacturing can be attained through a timely supply of materials on-site to avoid stacking. Contractors play an important role to execute manufacturing methods through smooth functioning.
9. Material Selection
Energy-efficient Designs are graded through LEED (Leadership in Energy and Environmental Design) certification. Architects and Clients opting for sustainable options can achieve LEED points by selecting materials from recycled products and Local markets.
Climatically responsive materials reduce thermal loss of the structure promoting Low carbon emission. Choosing locally available material responds to the climate and minimizes transportation emissions as well.
10. Proposing Renewable Energy Resources
Building’s operational energy accounts majorly for the carbon footprint. These operational energy functions can be sourced through renewable energy resources.
Using renewable energy for on-site construction phases and long-term solar interventions can reduce the demand for conventional energy resources. Though investing in renewable energy resources can be high in the initial cost. But certainly is affordable for long-term use and provides several subsidiaries.
Conclusion
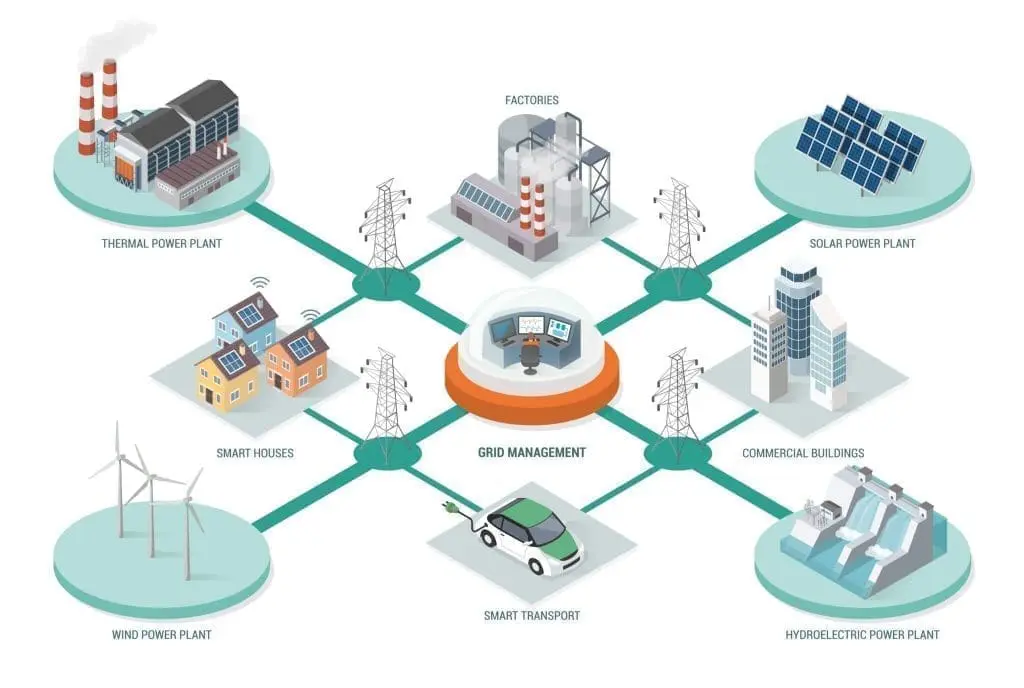
House construction processes emit a major amount of carbon emissions. These emissions contribute heavily to the carbon footprint of the building through embodied energy and operational energy demands.
It can be noted that dependency on conventional resources of energy like fossil fuels increases carbon emissions. However, It is practically not possible to immediately replace these resources. But reducing dependency through alternative renewable energy resources can reduce the carbon footprint of the building.
Carbon footprints are practical results of energy consumption and cannot be nullified. But the measures stated above can reduce the carbon footprint of your building during and after construction.
– Anshul Kulshrestha